IATF16949五大手册培训咨询课程五大工具培训—企业培训需求和培训机构合作请联系
非常您谢谢关注质量管理专家金舟军讲师IATF16949五大手册培训,更希望你选择我的培训咨询课程,上海科租企业管理咨询有限公司将为您提供专业、实战的IATF16949五大手册培训,保证您学完就会应用,要进一步了解过程FMEA培训详情,请马上与我本人联系,经考试合格发IATF16949五大手册培训证书,权威合格五大工具证书。
1.专业五大工具培训讲师--金舟军老师质量管理专家,精益质量创始人,二十年专业从事质量管理工具、五大工具培训和咨询。2.源自世界先进技术--金老师IATF16949五大手册培训咨询课程汲取原版手册、国际学术报告及论文、世界级企业五大工具例,国内领先水平。
3.采用客户案例实战--金老师IATF16949五大手册培训前书面、电话和客户现场调研,保证课程包括客户案例,使学员学完就会做。
4.学员实现最大价值--金老师自办IATF16949五大手册培训咨询公司,全部培训利润归老师所有,确保客户所有的钱都花在培训上,实现客户价值最大化。
培训的客户

金老师五大工具培训现场照片

金老师五大工具培训现场照片
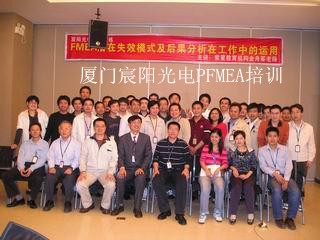
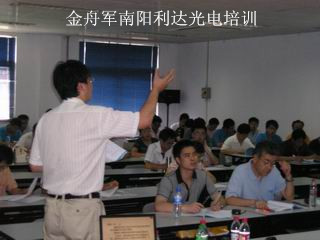
金老师IATF16949五大手册培训现场视频--点击图片即观看西瓜视频相应培训视频
金舟军老师MSA培训优势
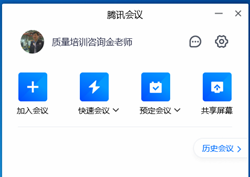
金舟军老师MSA培训优势
结合客户案例的实战型培训 包括后服务答疑的全过程
金舟军老师通过五大步骤结合客户案例讲解,确保学员学完全就会在工作中应用: 1 .案例网络调研、2.案例学员预习、3. 现场案例调研、4.案例练习点评、5.售后案例答疑。
1.案例网络调研
培训意向一经确定,金舟军老师就要与客户进行网络沟通,确定MSA实施难点,收集MSA实施资料,并就实施资料的细节进行沟通,并了解客户学习MSA的目的。
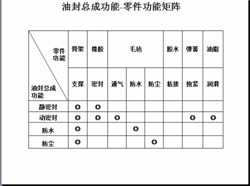
2.学员案例预习
金舟军老师根据MSA实施中的难点,事先为学员出MSA的预习题,帮助学员提前思考怎样解决实施案例的难点,同时也预习课堂讲解的知识。
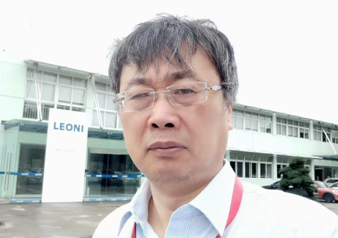
3. 现场案例调研
培训前一天,金舟军老师会到客户现场进行一天的现场调研,查找客户MSA实施情况,并为课堂针对客户实施MSA中的问题讲解做准备。
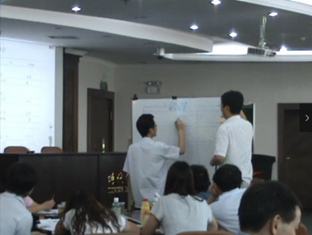
4.案例练习点评
根据案例实施中的难点问题,每天培训约有五十分钟的客户案例分组练习,每组学员的案例练习金舟军老师都要做详细的点评,确保学员学完全就会在工作中应用。
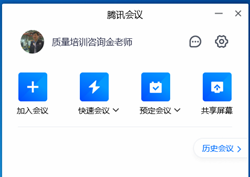
5.售后案例答疑
培训完成后一年之内,如果客户在实施MSA过程中有什么问题,可以为客户组织腾讯会议的在线答疑至少三次
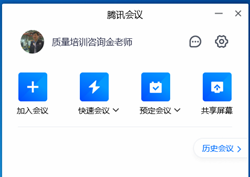
IATF16949五大手册培训
培训大纲
一.培训对象:项目管理人员、质量管理人员、检验人员、计量人员及工程技术人员。
二.培训目的:
1.掌握过程能力指数Cpk、过程性能指数Ppk和设备能力指数Cmk, 掌握Xbar-R控制图、单值和移动极差图和预控图。
2. 熟练运用PFMEA分析和评价本岗位或本工序潜在失效模式及后果分析,并能制定相应错误预防措施,以使所有过程的作业指导书源于该过程的PFMEA。;
3. 了解测量系统的测重复性、再现性、偏倚、线性、稳定性等五性,掌握minitab计算GRR并且能够解释结果。
4. 掌握APQP五个阶段输入输出要求和CP的方法,能应用APQP到制造责任工厂的项目开发工作中。
5. 掌握PPAP提交的要求。
三.培训大纲
一)SPC手册
1.统计过程的控制概述
产品三次设计
产品特性目标值与公差
质量特性的期望值
过程控制系统
变差的普通及特殊原因、
2.产品变差
直方图描述产品特性分布
基于分布分析原因
直方图MINITAB操作
3.正态分布总体参数估计
正态分布总体参数点估计
均值的无偏估计
总体方差的无偏估计
标准差的无偏估计
对估计量的评价
用Rbar方法估计
4.中心极限定理
样本均值的抽样变差
抽样分布--中心极限定理
总体为正态分布
5.质量损失函数
福特公司案例
美国产品与日本产品比较
“目标柱”思维方式VS损失函数思维方式
油泵柱塞损失函数
田口损失函数思维模型
两个质量指标-符合性质量和质量损失函数
损失函数与返修率
损失函数敏感程度
损失函数的减少
6.过程能力指数Cpk和过程性能指数Ppk
过程性能指数的提高
两种减少过程变差方法
过程控制-现场措施
过程改进-系统措施
现场不可控制的-普通原因变差
现场可控制的-特殊原因变差
过程能力—过程固有变差-普通原因产生过程变差σc
过程固有变差计算的两个条件
过程能力指数Cpk
过程能力指数Cpk和过程性能指数Ppk诊断过程
过程能力解释
Cpk和Ppk软件MINITAB操作
过程能力指数Ppk软件MINITAB计算的样本量与置信区间
7.戴明博士漏斗实验
漏斗实验四种调整规则
过程调整的两类錯误
什么是过度调整
过度调整案例
..........
二)MSA手册
1.测量系统基础
测量定义
测量应用
量具&测量设备
测量系统
测量结果-数据
计量型与计数型测量系统
讨论题-一个测量系统包括的范围
2.测量系统基本特征
分辨力
灵敏度
分辨力接受准则
读数原则
测量值科学记数法
讨论题-不对称公差分辨力接受准则
3.测量系统溯源
测量过程的目标-真值
基准值来源
溯源
校准&校准周期
讨论题-一个测量系统校准周期确定考虑的因素
4.测量过程变差
测量过程变差-S.W.I.P.E模型
测量系统数据质量
5.测量系统变差模型
普通的原因-特殊原因
测量系统的变差类型
准确度-偏倚
精确度-方差
讨论题-测量系统普通的原因导致什么测量变差
6.测量系统的变差五性
重复性Repeatability—EV设备变差
重复不好的原因
重复性计算
再现性Reproducibility--评价人间变差
再现性不好的原因
再现性计算
偏倚 Bias
偏倚不好的原因
线性Linearity
线性误差的可能原因
稳定性 Stability
不稳定的可能原因
讨论题-测量系统普通的原因导致什么测量变差
7.量具R﹠R或GRR
R&R 对过程变差计算的影响
R&R 对产品判定的影响
宽度误差R&R—接受准则
产品控制接受准则
过程控制接受准则
讨论题-只有上差的产品控制接受准则是什么
8.方差分析法(ANOVA)重复性和再现性GRR
与均值极差法比ANOVA的优点
方差分析法ANOVA方案
重复性计算
零件与评价人之间的交互作用计算
再现性计算
零件变差计算
minitab重复性和再现性GRR交叉研究应用
.........
三)FMEA手册
1. 产品制造和装配的控制
产品设计和开发VS产品制造和装配
过程方法
过程的要素及特点
过程的监视测量
过程特性&产品特性
产品特性-过程特性因果矩阵
关键产品特性KPC-关键过程特性KCC
案例演练-完成你所熟悉过程的产品特性-过程特性因果矩阵
2.过程控制
探测控制措施
产品检验
预防控制措施
过程控制系统
案例讨论-产品设计和开发与过程设计和开发的主要区别是什么
3. FMEA简介
PFMEA目的
PFMEA思维过程系统化 规范化 文件化
动态的PFMEA
案例讨论- PFMEA是怎样防止很多召回事件的发生
4设计FMEA步骤一:规划和准备
5. DFMEA步骤二:结构分析…
6.设计FMEA步骤三:功能分析
7.设计FMEA步骤四:失效分析
8.设计FMEA步骤五:风险分析
9.设计FMEA步骤六:优化
10..设计FMEA步骤七:结果文件化
11.四个主要顾客失效模式后果
过程潜在失效后果识别方法
失效的潜在起因/机理
根本起因五个方面
根本起因两个阶段
现行过程控制
工艺验证和SOP等控制方法
预防维护vs预测性维护
作业准备验证
标准作业
判断检验
信息检验
溯源检验
..............
四)APQP&PPAP手册
1.项目管理
项目管理简介
项目管理与APQP的关系
2.APQP产品质量先期策划简介
产品质量策划定义
APQP的目标
APQP之益处
APQP手册的目的
3.产品质量策划原理与工具
以顾客为关注焦点
质量功能展开QFD
基准确定
过程方法
过程开发&过程控制
特性矩阵图
关键过程特性&关键产品特性
过程流程图
概念设计&产品设计
预防缺陷
制造过程防错
设计防错系统
FMEA潜在失效模式及后果分析
同步工程
可制造性和装配设计
三次设计:结构设计 参数设计 容差设计
价值工程
精益生产
人机工程
FTA 可靠性设计
4.控制计划
控制计划目的
控制计划与作业指导书
控制计划与产品组
控制计划是动态文件
控制计划的益处
控制计划重点--过程分析
开发控制计划的信息与工具
控制计划开发流程
试生产控制计划和生产控制计划的区别
控制计划概述
控制计划栏目描述
样件控制计划、试生产控制计划和生产控制计划案例
...........
APQP产品质量先期策划
产品质量策划的基本原则
产品质量策划是一种结构化的方法,用来确定和制定确保某产品使顾客满意所需的步骤。产品质量策划的目标是促进与所涉及的每一个人的联系,以确保所要求的步骤按时完成。有效的产品质量策划领带于公司高层管理者对努力达到使顾客满意这一宗旨的承诺。产品质量策划有如下的益处。
本手册中所述的实际工作、工具和分析技术都按逻辑顺序排列,使其容易理解。
FMEA潜在失效模型及后果分析
FMEA的有效运用可建立过程预防和探测控制体系,FMEA有效实施是一切改进的前提条件汽车制造行业的FMEAs共有六类FMEA,其中SFMEA还可细分为产品SFMEA、过程SFMEA和设备SFMEA,FME作为风险评估工具,确保在产品和过程开发中识别潜在失效和确定预防措施分析方法。
SPC统计过程控制
控制图——过程控制的工具
贝尔试验室的Walter休哈特博士在二十世纪的二十年代研究过程时,首先区分了可控制和不可控制的变差,就是由于我们所说的普通及特殊原因产生的。他发明了一个简单有力的工具来区分它们——控制图。从那时起,在美国和其它国家,尤其是日本,成功地把控制图应用于各种过程控制场合。经验表明当出现变差的特殊原因时,控制图能有效地引起人们注意,它们在系统或过程改进要求减少普通原因变差时控制图能反映其大小。